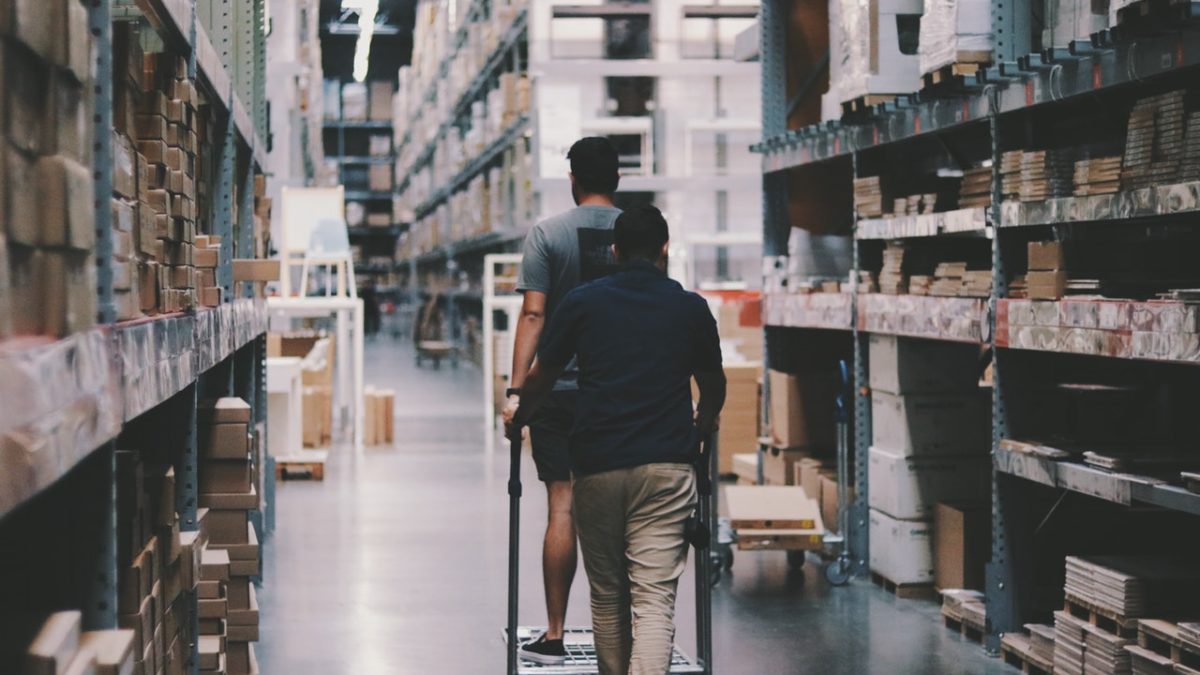
Warehouse Logistics Challenges
6 Ways to Surpass Snags in Warehouse Logistics
Continuous changes in technology and customer expectations may prove challenging when it comes to running a business. One of the biggest hurdles that businesses face is shipping products to customers in a timely fashion. As businesses grow, they often look to outside sources, like warehouse logistics companies, for help in managing and shipping inventory. Once inventory is moved offsite, it can create some additional logistic challenges for the company.
If you have recently felt the strain of warehouse logistics challenges, you are not alone. It is a common challenge that many businesses face because logistics includes managing people, inventory, and space. Here are some common warehouse logistics challenges you may face and recommendations on how to overcome them.
Inaccurate inventory count.
Tracking inventory is crucial to overall customer satisfaction as well as keeping cash flow positive. Not knowing how much you have of an item or having an inaccurate count logged can cause an unplanned shortage and unfulfilled orders. Instead of relying on team members to count and record items, which leads to more errors, businesses should consider inventory software.
Poor communication.
Communication is essential in maximizing productivity in warehouse logistics. Failure to communicate adequately with one another can result in delayed shipments, missing items in shipments, and even double items packed. All of these cost a company money. Utilize communication channels that make it easy to share updates with team members, so everybody is up to date.
Disorganized Inventory.
These days, warehouses are bigger than ever, making it a challenge to know where inventory is located. It is recommended that warehouse managers create a layout of the facility that identifies where specific stock is to be housed. When deliveries arrive, items should be moved quickly to their designated areas to prevent them from being overlooked and creating delays.
Inefficient warehouse layout.
A warehouse layout should also be efficient. If there are items that are frequently purchased together, it makes sense to keep these near one another. If they are on opposite ends of the warehouse, it costs businesses money because employees have to spend more time tracking down items to fulfill orders.
Demand fluctuations.
Most businesses experience different demands for specific products at various times throughout the year. Improper planning can cause inventory shortages and overages, which can cost your bottom line. The best way to overcome this is by utilizing historical data and sales to help predict future sales.
Hoarding products that don’t sell.
Finally, holding onto dead stock or items that don’t sell is a bad idea. It can be difficult for businesses to let go of items because of the investment. However, keeping items that don’t sell isn’t beneficial. Not only do they take up valuable storage space, but they also don’t bring any money in sitting there. Offer them as a gift with purchase or deeply discount the price to encourage sales.
Don’t let poor warehousing logistics prevent business growth or success. Econo-Courier helps businesses with warehouse logistics in addition to their shipping needs. Contact us for more information!
Recent Posts
Contact Info
75 Lackawanna Ave, Unit B
Parsippany, NJ 07054
Phone: (800) 526-9094